SKF offers all types of lubrication systems from single point lubricators to complex, fully-automated and centralized lubrication and oil circulation systems. SKF lubrication products are found in all industrial and vehicle systems, e.g. mining, railroad, machine tools, pulp & paper, wind power and marine equipment.
The benefits of correct, regular, measured lubrication as part of a fully managed maintenance programme cannot be overstated. Around thirty percent of premature failures in mechanical equipment are caused by poor or inadequate lubrication. Automating this process provides replenishment at the correct interval, at all the points where it is required and with the correct quantity. Minimal but adequate quantity lubrication can have major cost benefits and offers substantial environmental benefits over less precise traditional techniques.
SKF Lubrication System consists of the former companies VOGEL and Safematic and provides all their knowledge within lubrication solutions.
You can find information about SKF’s lubrication products and systems below Maintenance product offers andLubrication systems on SKF.com
Single-point automatic lubricator
Advantages of the central lubrication system
Single-point automatic lubricator
The SKF SYSTEM 24 is a single-point automatic lubricator that can be used to supply grease to single lubrication points that are usually lubricated by means of a grease gun.
SKF SYSTEM 24 lubricators can be set to provide the correct quantity of lubricant over a set time period. This enables more accurate control of the amount of lubricant supplied compared to traditional manual re-lubrication techniques. The SKF SYSTEM 24 is excellent for applications that are difficult to reach with a grease gun, or where a large number of greasing points mean that manual greasing techniques would be less effective.
Advantages of the central lubrication system
The central lubricating system offers the following advantages:
-
Higher productivity resulting from increased life and reduced shutdowns.
-
Reduced operating costs resulting from a lower consumption of energy (lower friction), spare parts, lubricants and labour costs resulting from reduced requirements for maintenance and operation.
-
Reduced wear resulting from dosing regularly and automatically precise and controlled quantities of a lubricant within short intervals over the operation of the machine.
-
Elimination of the risk that some lubricating points are over-lubricated and others are neglected.
-
Elimination of lubricant contamination.
-
Increased safety because the operator does not need to be in the vicinity of difficult-to-reach and dangerous areas of the machine (e.g. ovens, cranes, harvesting machines, chemical).
-
Maximum cleanliness is achieved.
-
Environment-friendliness results from the usage of minimum quantities of lubricants and handling.
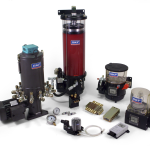
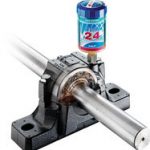
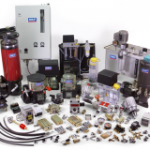